Vacuum packing vs Gas flushing- Ask the experts
08/04/2021
At Flexipol, we're dedicated to provide our customers with as much knowledge as we can, so we asked some of our technical experts all about the barrier packaging industry and the differences between choosing vacuum packing vs gas flushing processes.
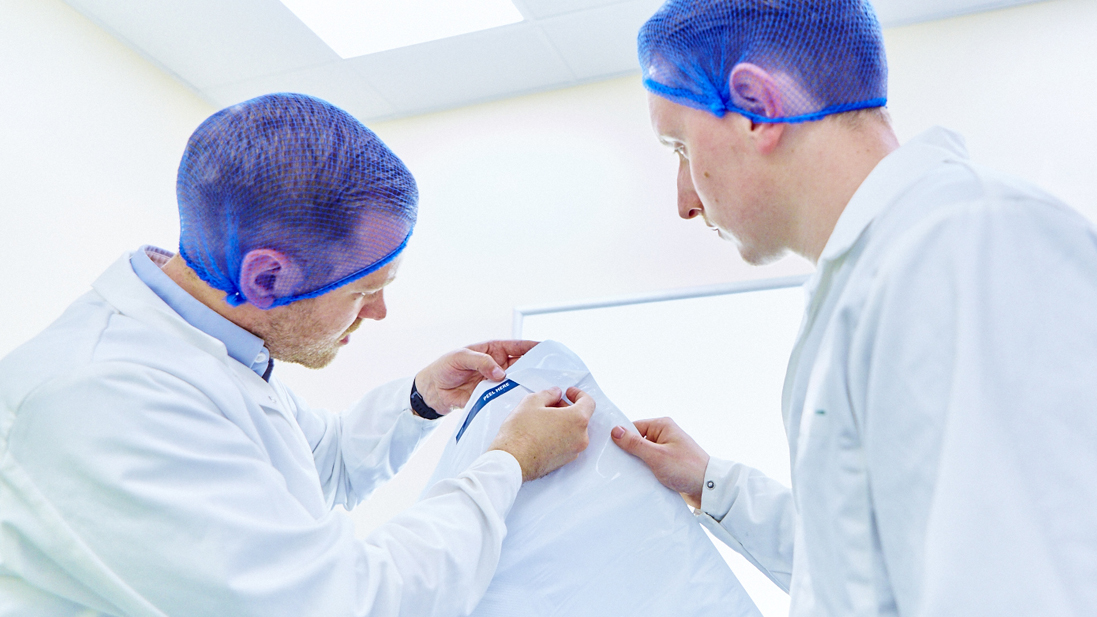
At Flexipol, we’re dedicated to provide our customers with as much knowledge as we can, so we asked some of our technical experts all about the barrier packaging industry and the differences between choosing vacuum packing vs gas flushing processes.
Vacuum packing vs Gas flushing?
Vacuum packing removes air and oxygen around a product, leaving no chance for mould or bacteria to spoil food or corrode metals. It’s an inexpensive process to extend shelf life on perishable products.
Best suited to meat, fish and hard cheese, it can be small or large scale. Chamber machines can be compact and table top, or larger with swing lids.
Smaller scale industries like butchers’ shops benefit from vacuum packing as it’s a quick, cheap way of protecting products. A chamber machine is an entry level investment and the bags are inexpensive and scalable. To change products, all that is needed is to switch to a different size or thickness of bag depending on requirements.
Red meat is favourable with vacuum packing as it is generally packaged as an end product, whereas gas flushing is associated more with poultry. However, some products can go through both processes. For example, abattoirs vacuum pack meat to transport it, then it will be re-packed and gas flushed in a tray at supermarkets, extending shelf life again.
The process of gas flushing removes all oxygen, and flushes the pack with an inert gas, like CO2 or Nitrogen.
Gas flushing is suited to large scale production as machinery is bulky and expensive. Well suited to whole birds as vacuum packing can’t remove the air from inside the cavity. It also is better for soft products such as cheeses and bakery products, which would be squashed in a vacuum environment.
Current industry trends?
There is a large demand for recyclable, compostable and biodegradable materials. A new recyclable material is available with less than 5% EVOH, it’s thicker than standard materials, and approx. 20% more expensive.
There is a drive for thinner films, still ensuring uncompromised performance, to tackle plastic consumption and waste. Advancement in film technology mean that bags can be stronger and thinner, reducing packaging waste, and cost advantages.
Despite the initiatives for greener packaging, aesthetically pleasing packaging hasn’t become less popular. Consumers are still concerned with their product’s packed appearance, with parchment film and printed bags still popular.
Common pitfalls to avoid?
- Buying off the shelf without advice from a technical expert. This leads to acquiring unsuitable bags, which could result in rejection of stock being not fit for purpose by end consumers.
Each product has specific requirements, e.g bone-in products or circuit boards require a different material than a standard bag, to withstand strains like sharp edges.
- Not understanding the correct process for each application. Buying a gas flushing machine for a product better suited to vacuum packing can slow down the process and spoil presentation.
- Not running packaging trials. All packaging should be tested before committing. The key is speaking to industry experts and getting advice first.
What to expect if you’re looking for a new supplier?
Suppliers should guide customers through decisions in their process, offering advice as specialists in the barrier packaging industry.
They should value engineer current packaging requirements, making them more cost effective and environmentally friendly, whilst reducing waste and excess packaging where possible.
They should have expertise of consumers on all scales in different industries, from food, to industrial. This means they can offer the best packaging solution.
Dealing directly with a manufacturer is the easiest way to guarantee receiving the correct packaging. They are closer to the process and can be reactive to any changes.
In summary, consumers should ensure their supplier can understand the process from start to finish, so the products offered are high quality and right first time.